This is the UK IDEA Engineering Scale CO2 Absorber. It was designed, installed, operated and analyzed since 2011, with funding primarily from U.S. Department of Energy National Energy Technology Laboratory through Cooperative Agreement DE-FE0007395, in Research Partnership with PPL Corporation, and with other funding and support received from PPL Corporation, Duke Energy, Electric Power Research Institute, Inc., Kentucky Power and the Kentucky Department for Energy Development.
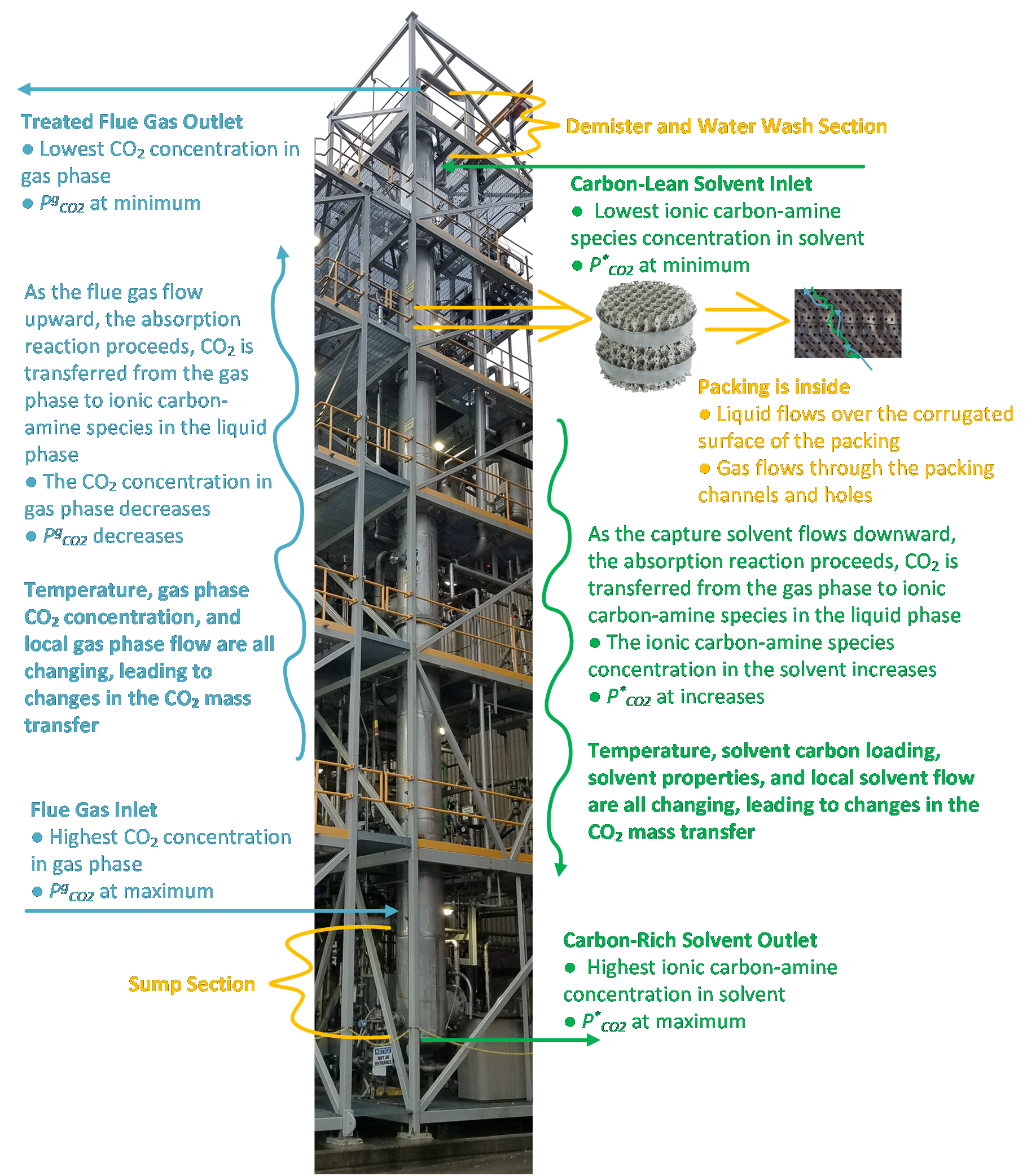
Inside the absorber column is where the CO2 is transferred from the flue gas to the capture solvent.
The flue gas enters toward the bottom of the column, above the sump section, and flows upward, while the carbon-lean capture solvent enters toward the top of the column, below the demister and water wash sections and flows downward. Where the CO2 in the gas phase encounters an amine group in the liquid phase, a chemical absorption reaction occurs. The CO2 combines with the amine to form ionic carbon-amine species in the liquid phase. The concentration of the ionic carbon-amine species in the solvent is referred to as the carbon loading. When the capture solvent first enters the absorber, it is referred to as carbon-lean, meaning it contains very few ionic carbon-species. As the carbon-lean solvent travels down the column, more and more CO2 is absorbed by the solvent, and more and more ionic carbon-amine species are formed within. When the solvent collects in the sump section of the absorber, it is referred to as carbon-rich, meaning it contains many ionic carbon-amine species. The chemical absorption reaction is exothermic, meaning one of the products is heat and as CO2 absorption reaction proceeds, as CO2 is transferred from the flue gas to the capture solvent, the temperature increases.
The CO2 concentration in the gas phase is highest at toward bottom of the column, where it enters, and decreases as flue gas flows upward. The concentration of ionic carbon-amine species is lowest toward the top of the column, where the carbon-lean solvent enters and increases as the solvent flows down. The absorption reaction is fastest toward the top of the column and a temperature bulge results in the top portion. Temperature is often controlled with one or more intercoolers along the column height.
So, the gas phase CO2 concentration, the solvent carbon loading and the temperature all change throughout the absorber column.
The mass transfer of the CO2 from the flue gas to the capture solvent is defined by this Equation 1.
Equation 1.
Gas Mass Transfer
Here gas is CO2, A is the contact area between the gas and the liquid; KG is the overall mass transfer coefficient and; is the difference between the gas phase partial pressure of CO2, , and the equilibrium partial pressure of CO2 resulting from the loading in the solvent, . This difference in partial pressure terms is referred to as the driving force for CO2 capture. Increasing any, and all, of these terms is how mass transfer in the absorber is increased.
The area, , is often manipulated by the column internals, such as packing, which provide a physical place for liquid and gas to come into contact. Different kinds of packing can be applied, but always with a trade-off between efficiency and capacity. But is also affected by local solvent and gas flow rates and the solvent properties such as hydrophilicity, viscosity, surface tension. The solvent properties are affected by the carbon loading and temperature. Likewise, the mass transfer coefficient, , is affected by diffusion of the CO2, the amine concentration, and the absorption reaction chemistry, all of which are also affected by carbon loading and temperature. Finally, the driving force for CO2 absorption is affected by gas phase CO2 concentration, the solvent carbon loading, and the temperature.
Analogy to WFGD
The CO2 absorber has similarities and differences when compared to wet flue gas desulfurization units (WFGDs) already applied at coal-fired utilities, as summarized below.
Coal Fired Power Generation SO2 Scrubber and CO2 Absorber Configurations and Operating Parameters. | ||
Aspect | WFGD | CO2 Capture |
Flow Configuration | Counter-current | Counter-current |
Inlet Concentration | 3000-5000 ppm SO2 | 10-13 vol% CO2 |
Outlet Concentration | 10-50 ppm SO2 | 1.5-2 vol % CO2 |
Absorbing Chemical Concentration | 0.026 mol/m3 Ca2+ | 1200-1500 mol/m3 amine |
Column Internals | Spray (with/out tray) | Film on packing |
Gas Velocity | 10-15 ft/s | 3-6 ft/s |
L/G (mass/mass) | 10 | 3.5 |
Temperature Profile | Top 55, bottom 60 oC | Top 40, middle 70, bottom 50 oC |
Effective Wet Surface per Unit Volume | 1523.85 m2/m3 | 200 m2/m3 |
Diffusivity | 1.2x10-5 m2/s | 2.0x10-9 m2/s |
Reaction Kinetics, K2 | 10000 m-2 | 3000 m-2 |
Log Mean Driving Force | 0.07 kPa | 4.33 kPa |
Starting with A from Equation 1. The WFGD applies a spray of limestone, Ca2CO3, slurry while solvent distributed and flowing over structured packing is applied in the CO2 absorber. The FGD spray droplets are ~150-200 µm and the limestone slurry to gas mass flow ratio is ~10. The liquid/gas specific surface area is ~1500 m2/unit volume. But for 250Y structured packing, commonly applied in the CO2 absorber, the surface area is only 200 m2/unit volume.
Considering KG from Equation 1. The overall mass transfer coefficient, capital KG, is a function of both the gas phase mass transfer, kg, and the solvent mass transfer, kg', as shown in Equation 2. Gas phase mass transfer is much faster than liquid phase, which is to say that overall mass transfer is limited by the liquid phase mass transfer.
' is a function of diffusion, , reaction kinetics, K2, the absorbing species concentration, [solvent], and the Henry’s constant, as shown in Equation 3.
Equation 2.
Equation 3.
The calculated value of for CO2 and a fast solvent, like piperazine (PZ) is about twice as that for SO2 scrubbing. We must also remember the great difference in the Ca2+ and amine concentrations, by 5 orders of magnitude, which favors CO2 absorption mass transfer.
The diffusivity of CO2 within the liquid is lower than that for SO2, disfavors CO2 absorption mass transfer. The reaction kinetics for CO2 absorption are much lower than for SO2 absorption, disfavoring CO2 absorption mass transfer.
Finally, consider the driving force for absorption. The vast difference in the inlet and outlet concentrations, 10-50 vol% to 1.2-2 vol% for CO2 capture and 3000-5000 ppm to 10-30 ppm for SO2, result in a much smaller driving force for SO2 absorption.
With SO2 absorption there is high surface area, higher SO2 diffusivity, fast kinetics, but a low reactant concentration and low driving force. For CO2 absorption, the opposite is the case. There is a low surface area, low CO2 diffusivity, slow kinetics, high reactant concentration and high driving force.
Analogy to a Cooling Tower
As warm water flows down over packing and ambient air is blown upward through and over the water, the water evaporated. The phenomenon of evaporative cooling is what makes a cooling tower work. The same happens inside the CO2 absorber. Water from the CO2 capture solvent evaporates as it flows down over the flue gas. Evaporative cooling does also occur within the CO2 absorber.
Quiz
- What is inside the CO2 absorber?
- What are three main variables affecting CO2 capture?
- What other conditions and properties affect CO2 capture?